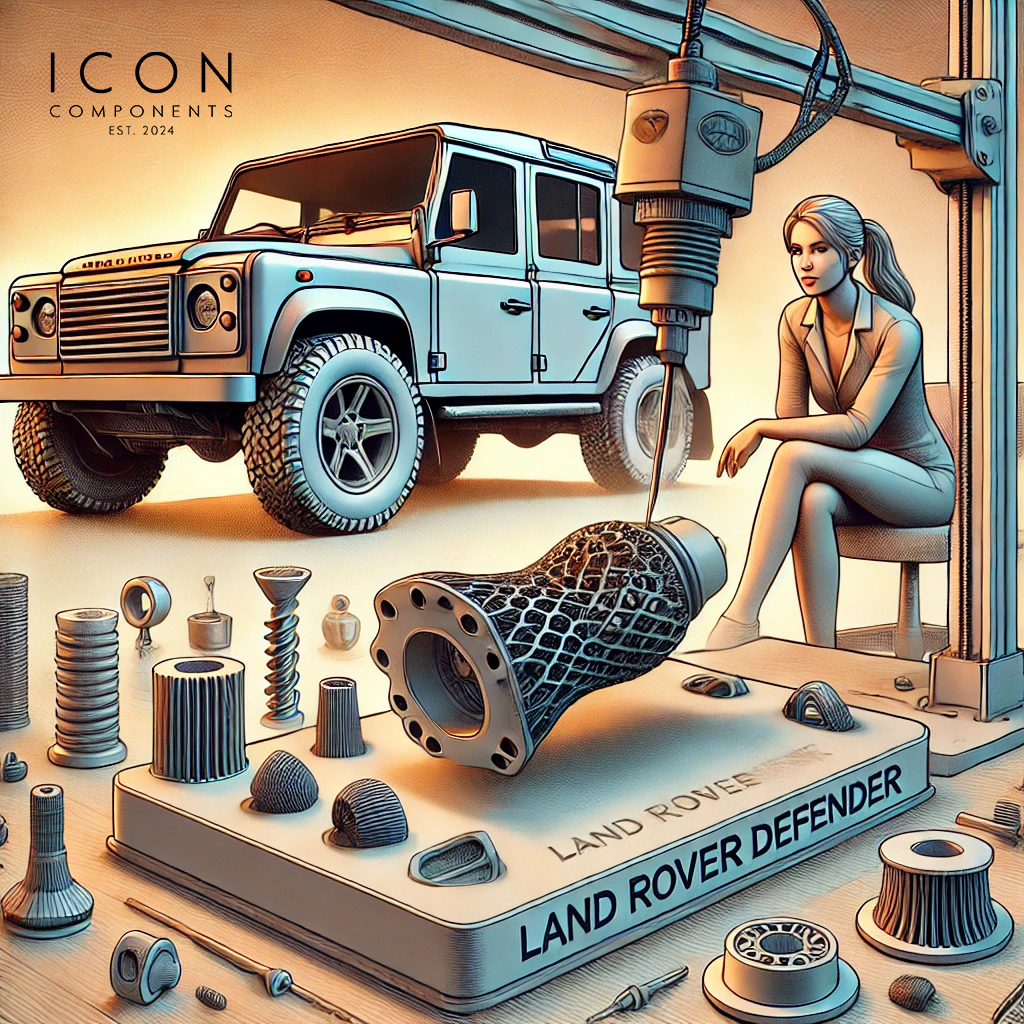
How 3D Printing is Transforming Custom Car Part Manufacturing
The automotive industry is rapidly evolving, and one of the most exciting technological advancements shaping its future is 3D printing. From prototyping to full-scale production, 3D printing is revolutionizing the way car parts are designed and manufactured. For car enthusiasts and those looking to customize their vehicles, this new technology opens up a world of possibilities, allowing for highly personalized and precise components.
In this blog post, we will explore how 3D printing is transforming custom car part manufacturing, and specifically, how Icon Components is utilizing this cutting-edge technology to offer bespoke parts for Land Rover Defenders.
What is 3D Printing?
3D printing, also known as additive manufacturing, is a process where material is added layer by layer to create a three-dimensional object based on a digital model. Unlike traditional manufacturing methods, which involve cutting away material to shape parts, 3D printing builds up a part by layering materials such as plastics, metals, and composites.
This method allows for incredibly precise and intricate designs that would be difficult, if not impossible, to achieve with traditional manufacturing techniques. For the automotive industry, 3D printing enables faster prototyping, greater customization, and more efficient production processes.
Advantages of 3D Printing for Custom Car Parts
1. Precision and Customization
One of the key benefits of 3D printing is the ability to create bespoke parts that are tailored to specific needs. Whether you’re restoring a vintage Land Rover Defender or upgrading a modern model, Icon Components offers custom parts that are designed to fit perfectly, improving both performance and aesthetics. With 3D printing, every aspect of the part can be fine-tuned, ensuring that it meets exact specifications and enhances the functionality of the vehicle.
For example, custom decals, body trims, and interior elements can be designed with precise detail, giving your Land Rover Defender a truly unique look. Whether it's a custom shift lever bush or a dash mount for handheld radios, 3D printing allows for customization to meet individual tastes and requirements.
2. Faster Prototyping and Development
Traditionally, creating prototypes for car parts involved time-consuming processes, including casting molds and machining. With 3D printing, however, parts can be prototyped quickly and inexpensively, allowing designers to test and modify components in real-time. This enables faster development cycles and the ability to iterate designs before mass production.
Icon Components uses 3D printing to prototype and test new parts for Land Rover Defenders. By using this technology, the company can refine designs, ensuring they meet high standards of durability and functionality before offering them to customers. This accelerated prototyping process allows Icon Components to offer high-quality, custom-made parts that are ready for production and distribution more quickly.
3. Reducing Costs for Low-Volume Production
For custom or low-volume parts, traditional manufacturing methods can be prohibitively expensive. The need for specialized molds, tooling, and labor can add significant costs to the production process. With 3D printing, these costs are reduced, making it more affordable to produce small runs of bespoke parts for specific models or individual needs.
For example, creating brake line clips or bonnet hinge bushes for older Defender models might not justify the cost of mass production, but 3D printing makes it possible to manufacture these components in small quantities at a fraction of the cost. Icon Components utilizes 3D printing to keep costs manageable while still offering high-quality parts for enthusiasts who want to restore or modify their vehicles.
4. Enhanced Durability with Innovative Materials
3D printing isn’t just about creating parts faster and cheaper; it’s also about innovation in materials. While traditional parts may be made from standard metals or plastics, 3D printing opens the door to a wide variety of materials that can be tailored for specific applications. For example, parts can be made from high-strength composites, titanium, or carbon fiber, all of which offer superior durability and weight-saving advantages.
At Icon Components, 3D printing allows the use of innovative materials for custom parts that must endure the toughest conditions. Whether it's a custom body trim designed to handle extreme off-road conditions or a durable dash mount that holds up to rugged use, 3D printing ensures that every part is built for longevity.
5. Sustainability Benefits
The automotive industry has increasingly focused on sustainability, and 3D printing aligns perfectly with this trend. Traditional manufacturing processes often generate a significant amount of waste material as parts are cut, molded, and shaped. With 3D printing, material is used only where it's needed, significantly reducing waste.
Additionally, the ability to produce on-demand means that parts are created only when needed, helping to minimize overproduction and reduce the carbon footprint of manufacturing. Icon Components embraces these sustainability benefits, making it easier to produce eco-friendly custom parts for customers who are conscious of their environmental impact.
How Icon Components Utilizes 3D Printing in Custom Land Rover Parts
At Icon Components, 3D printing plays a vital role in enhancing the customization and functionality of Land Rover Defender parts. By leveraging this technology, Icon Components is able to offer one-of-a-kind parts that cater to the unique needs of Defender owners. Whether you’re looking to restore a vintage model or upgrade a modern one, 3D printing provides an efficient and cost-effective solution to meet your needs.
The company is committed to producing high-quality, precision-engineered components that fit perfectly with Land Rover Defenders. From shift lever bushes to body trims and even stickers and decals, Icon Components ensures that every custom part is designed with durability, precision, and aesthetics in mind.
Conclusion
3D printing is not just a passing trend—it is transforming the way car parts are designed, manufactured, and customized. With its ability to offer precision, customization, and cost-efficiency, it has become an essential tool for car enthusiasts who want to take their vehicles to the next level.
At Icon Components, 3D printing enables the creation of bespoke parts for Land Rover Defenders, ensuring that each component is tailored to meet the specific needs and preferences of the customer. Whether restoring a vintage model or upgrading a modern Defender, 3D printing is helping bring innovative solutions to the world of automotive customization.
To explore the full range of custom Land Rover parts and accessories, visit Icon Components today and discover how 3D printing is shaping the future of automotive parts manufacturing